Emboss Tower: Embossed Structural Skin for Tall Buildings
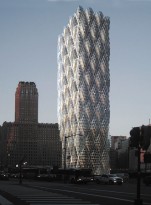
The article deals with the function of a structural skin with an embossed surface applicable to use for tall building structures. The major diagrid system with a secondary embossed surface structure provides an enhanced perimeter structural system by increasing tube section areas and reduces aerodynamic loads by disorienting major organized structure of winds. A parametric study used to investigate an optimized configuration of the embossed structure revealed that the embossed structure has a structural advantage in stiffening the structure, reducing lateral drift to 90% compared to a non-embossed diagrid baseline model, and results of wind load analysis using computational fluid dynamics, demonstrated the proposed embossed system can reduce surface wind load. The resulting undulating embossed skin geometry presents both opportunities for incorporating versatile interior environments as well as unique challenges for daylighting and thermal control of the envelope. Solar and thermal control requires multiple daylighting solutions to address each local façade surface condition in order to reduce energy loads and meet occupant comfort standards. These findings illustrate that although more complex in geometry, architects and engineers can produce tall buildings that have less impact on the environment by utilizing structural forms that reduce structural steel needed for stiffening, thus reducing embodied CO2, while positively affecting indoor quality and energy performance, all possible while creating a unique urban iconography derived from the performance of building skin.
INTRODUCTION: THICKNESS OF BUILDING ENVELOPE
It has been more than 100 years since Le Corbusier designed the Dom-Ino system, an open floor plan prototype which signalled the liberation of architecture from the burden of exclusively designing structures with load bearing skins. This ‘free façade’ capable of hanging non-structural material to the envelope has become the standard of the building industry in the 21st century. The market driven culture and supply chain to the building industry has become highly sophisticated in the production of these curtain wall related systems. The transparency of non-load bearing skin systems fuelled by a universal culture of modernism has become the exclusive building system for buildings that now dominate the skyline of all major global cities. However, the resulting decreased thermal mass in the production and on-site application of aluminium curtainwall systems, and societies growing concern for reducing the building industries impact on the environment, has contributed to the development of products to be added to curtainwall systems rather a rethinking of the tall building system as a whole. Increasingly stringent minimum efficiency energy standards call for improved thermal performance of the building envelope as well as solar controls, however the standardization of solutions results in a common architectural response to a climate, building type, and orientation. Often, when budgets cannot accommodate high performance glazing or external shading systems across these large façades, the window to wall ratio is often adjusted making for the right U-factor for meeting local codes. In contrast to the standardization of solutions, digital design and fabrication tools, and advances in material research are contributing to the “return of ornaments” in the building skin, argued to be the new type of subjectivity characteristics of the digital age (Picon, 2014).
Full content of this issue you can read here
The full version of the article can be read in our printed issue, also you can subscribe to the web-version of the magazine
Authors: JIN YOUNG SONG, DEPARTMENT OF ARCHITECTURE, UNIVERSITY AT BUFFALO, THE STATE UNIVERSITY OF NEW YORK; DONGHUN LEE, LESLIE E. ROBERTSON ASSOCIATES; JAMES ERICKSON, ARIZONA STATE UNIVERSITY; JIANMING HAO AND TENG WU, DEPARTMENT OF CIVIL, STRUCTURAL AND ENVIRONMENTAL ENGINEERING, UNIVERSITY AT BUFFALO, THE STATE UNIVERSITY OF NEW YORK; BONGHWAN KIM, SKIDMORE, OWINGS & MERRILL LLP